MECHATRONICS

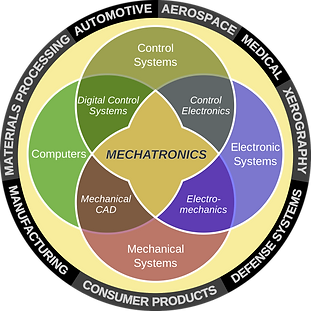

Mechatronics is a multidisciplinary field of engineering that includes a combination of systems engineering, mechanical engineering, electrical engineering, telecommunications engineering, control engineering and computer engineering dealing with the design of the products whose function relies mostly on the integration of mechanical and electronic components coordinated by a control architecture.
There are limitless innovations that can be done with mechatronics.
You can see in the ENGINEERING page about the courses I took in this
field or EDUCATION page for relevant schools.
I started working on this area when I was in Sabancı University
Summer School by taking the course Mechatronics and Humanoid Robots
from Prof. Mustafa Ünel. After that I went for another summer school, but this
time it was from Festo, a German company that leads the industrial mechatronics
technologies all around the world. They have an education department called Didactic
and I took Programmable Logic Controller (PLC) from Ed. S. Hakan Öztürk; Servo Motors and Drivers from Assist. Prof. Dr. Özgür Yılmaz; Industrial Electrics, Sensors, Pneumatics from Ed. S. Emin Dinç and finished Mechatronics Application Project from Yavuz Eminoğlu.
It was not until my third year of my B.Sc. in Özyeğin University that I started taking mechatronics courses and working in the robotics lab for related projects. I am currently studying M.Sc. Mechatronics Engineering in Department of Electrical Power Engineering and Mechatronics at Tallinn University of Technology (TTÜ). I had an exchange year in RWTH Aachen University to have more intense mechatronics, control and robotics within the electrical and mechanical departments. I am still following the related works from IEEE.
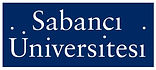

Research and Development of an Upper-Body Exoskeleton
During my Master studies in Tallinn University of Technology (TalTech), I started working on an exoskeleton research with a team and supervisors. It started as an lifting solution project for an industrial plant but shortly it took a turn to a specific topic which is an upper-body exoskeleton. Then it became a fully academic project with the related company leaving the project. This project is continued with more than one section with different parts. Below, you can find short information on these sections as parts of this big project.

Exoskeletons for Human Performance Augmentation Seminar
This section of the project was a basic preliminary research and it's presentation. It was prepared as a course seminar with a team and it's aim is to explain the reasons behind the topic selection as well as giving a background information on the related concepts. It includes information from several historical and current industrial applications of exoskeletons and their relation with human augmentation projects.
Wearable Upper-Body Exoskeleton for Production Workers
This section of the project represents the actual beginning of the project with a comprehensive research on the topic. It was done under the supervision of Mart Tamre from TalTech as a Mechatronics and Smart Systems Project . It was a team effort and prepared within almost four months. After the preliminary direction, there was a detailed literature review and industry research. Abstract of the report can be seen below. We also studied several engineering standards and software tools. The work done includes a simple process simulation within a factory, some basic design approach on the exoskeleton, and human-machine interaction analysis software evaluation. We also considered several future works like a potential motion study or mechanical analysis of the exoskeleton. The report and the presentation as the defense of the work can also be found in the related links.
ABSTRACT - This report is prepared to describe the work done on a research on exoskeletons for human performance augmentation in industrial applications. The preliminary direction was focused to find a general solution to avoid heavy lifting injuries of a certain factory’s employees. However, the direction of the project was changed to specifically wearable upper-body exoskeletons for production workers. After a detailed literature review and industry research with specific focus on relevant engineering standards. The software tools were decided on, to complete the planned tasks and most of them were used during the practical phases. A basic process simulation of working environment and initial design of exoskeleton model was prepared. Relevant evaluations were conducted in motion studies and human-exoskeleton interaction analysis, on a theoretical aspect. The results of the research and work done were very successful, however, they can be improved. Due to various constraints, several sections were not completed, such as mechanical analysis or design improvements. Therefore, they will be conducted as future progress with less time and budget limitations.
Controlled Motion Simulation of an Exoskeleton Model
This section of the project is a simple work done as a motion study of the basic design prepared in previous section. The purpose of this work is to perform a motion study using several software tools, and to obtain a final simulation of the working conditions of the developed exoskeleton model.It was completed with the same team and supervisor as an Advanced Robotics project. The tools and design are pretty much the same but with the motion study, there was an addition of a load to model. Multidomain model of the design is also obtained with research on certain motors and parameters. The simulation results were as expected.
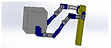

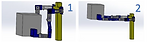


Research on Upper-Body Exoskeletons for Performance Augmentation of Production Workers
This section of the project is the publication of the work done and planned for the future. It includes a shorter version of the research done in previous sections. Also, the development of the exoskeleton is covered in many aspects just like the work done before. The paper consists of plans for the future work also as mentioned before. The publication was done within the proceedings of the 30th Danube Adria Association for Automation & Manufacturing (DAAAM) International Symposium (dpn: 74075) in Zadar, Croatia. We also prepared and presented a poster during the symposium. In addition, we had an oral presentation to explain our work. We were awarded with best oral presentation voted by experts of DAAAM 2019. The paper will be available with the rest of the proceedings of the 30th DAAAM International Symposium on Intelligent Manufacturing and Automation, published by DAAAM International, ISSN 1726-9679, Vienna, Austria.
Abstract
Exoskeletons are wearable devices that are widely used in various fields as; medicine, military, or industrial applications for human performance augmentation. They are highly complex systems and mostly used for specific purposes such as handling certain weights. Since this paper is concerned with the latter, therefore, a detailed literature review and industry research, with specific focus on relevant engineering standards has been conducted. The necessary software tools were chosen to complete a basic simulation of the working environment and initial design of an exoskeleton model. Relevant tool evaluations were conducted, in terms of motion studies and human-exoskeleton interaction analysis, on a theoretical aspect. The results of the conducted research, design, and simulations were successful, with a room for future improvement including several sections such as mechanical analysis or design improvements.
Keywords: Exoskeleton; Human Augmentation; Upper-body; Human-Machine Interaction

Development of an Upper-Body Exoskeleton
This section of the project is the Master Thesis prepared for Tallinn University of Technology. The poster, presentation, and report is accessible from clicking the images below. The thesis is stored in the digital library of the university as well for anyone in the network to access freely. The preface is given below to explain it shortly. For more information, without reading the whole report, you can check the introduction and summary chapters.
This Master Thesis is initiated by F. Ozan Dengiz for the completion of studies on Mechatronics Engineering with a genuine topic. It is concluded in Department of Electrical Power Engineering and Mechatronics within the Engineering Faculty at Tallinn University of Technology (TalTech). The major thesis work is done solely by the author within the mentioned university.
A number of people who got included in various phases of the project deserves gratitude. Many thanks to Mohamed Abdelmomen, Hoda Samir, and Hakan Demir who previously worked in this project. Also, major acknowledgements should be given to the thesis supervisor Anton Rassõlkin for his feedbacks on the report. Moreover, support of the programme director Mart Tamre made it possible to work on this topic from the beginning. In addition, numerous researchers from several universities including TalTech, RWTH Aachen, and Aalborg University helped on certain aspects of the development process.
This work is completed as a part of an exoskeleton project that was started to solve a specific problem. The scope of this thesis covers the research and development of a lightweight mobile active upper-body exoskeleton for industrial workers who are lifting heavy loads on daily basis. It shall be a powered electromechanical device to decrease the musculoskeletal fatigue on the user with human augmentation properties.
This thesis includes a comprehensive literature review on exoskeletons, mainly focusing on active upper-body models including many industrial and academic research projects. The current international standards related to exoskeletons with relation to robots are also examined. The interaction between human and exoskeleton is investigated by focusing on kinematics and physical interaction. Powering the exoskeleton and the communication plans are also explored for this specific device. A certain design is proposed including selection of materials, cross-sections of rigid parts, and overall joints. The control approach to the developed exoskeleton is described with chosen components as well as functional diagrams and algorithm charts. Numerous figures, tables, graphs, etc. are used to clarify crowded topics both in the thesis body and appendices at the end.
Keywords – Research, development, upper-body, exoskeleton, master thesis
Research and Development on Mobile Powered Upper-Body Exoskeletons for Industrial Usage
This section of the project is the publication of the work done in the previous thesis section. It includes a shorter version of the research done in previous sections. Also, the development of the exoskeleton is covered in many aspects just like the work done before. The publication was done within the proceedings of the 21st International Symposium INFOTEH-JAHORINA (INFOTEH) in East Sarajevo, Bosnia and Herzegovina (ID: 4). I prepared and presented the work online during the symposium. The paper is available with the rest of the proceedings (VRT-1.1) as well as in IEEE Xplore with DOI: 10.1109/INFOTEH53737.2022.9751255 online.
Abstract
This work is completed as a part of an exoskeleton project that was started to solve a specific problem. The scope covers the research and development of a lightweight mobile active upper-body exoskeleton for industrial workers who are lifting heavy loads on daily basis. It shall be a powered electromechanical device to decrease the musculoskeletal fatigue on the user with human augmentation properties. There will be certain constraints such as body part, mobility, and activity. The proposed design is the most optimized version that can be produced with the current state of the related studies.
Keywords: Exoskeleton; Upper-body; Research; Development
PLC Interface - Pump Control System
One of the assignments given in a Control course during my Master studies was to create a control algorithm for a certain task using a Programmable Logic Controller and visualize the panel for the operator. I used ABB Automation Builder to write the code and CoDeSys for visualization. The purpose was to control the liquid level of a tank in any case including overflow, drainage or extreme emergency situations. Assignment was a success. The inputs from PLC gave the correct outputs through the interface. My system was able to control any disturbance and it visually easy to handle. You can see the front panel on the right side.

One of the courses I took in my Bachelors required to build a simple mechatronics setup and to write a short paper about it. It was a team effort, at least on the experimental parts, to work on this task. My project design can be seen on the right side. It was an experiment on a basic setup for measuring the force applied with a Festo fluidic muscle and analysing the input output relationship to work on the current muscle technology. I named the paper Setup of Force Measurement System Using a Fluidic Muscle. You can find the abstract and the download button below.
Abstract— This paper presents a very basic transportable electro-pneumatic system with a setup specifically designed to hold the fluidic muscle and regulator used in the experiment. To measure the force of the artificial muscle a load cell is used. The data were gained by the NI hardware. We aimed to find out formulas of the fluidic muscle on the input-output analysis of the force.
As a result the tests showed that there are needs for more tests to obtain a decent formula for this task because of the limited range of the items used in this experiment. But we concluded on the fact that there can be some common equations for the results. Therefore the fluidic muscle system was regarded as being useful in various tasks that will be target in the future.
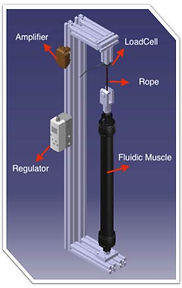